More than five billion trees are cut down every year for paper, packaging and fashion. Many of them are in ancient, old-growth forests that are not just rich in biodiversity but are crucial carbon sinks that absorb massive amounts of the C02 we belch out every year.
But what if you could take the mountains of clothes and paper that are discarded and turn that into clothes and paper again, leaving those endangered forests alone to do much more important work?
It’s already happening. And a major cash investment into a Canadian non-profit is designed to help scale up this innovative engine of the circular economy at a critical time in climate action.
Last month, Vancouver-based Canopy received US$60 million from The Audacious Project, a funding initiative affiliated with TED Talks, to accelerate the commercial-scale production of fabrics, pulp, paper and packaging from textiles and food scraps that usually end up in landfills or are burned.
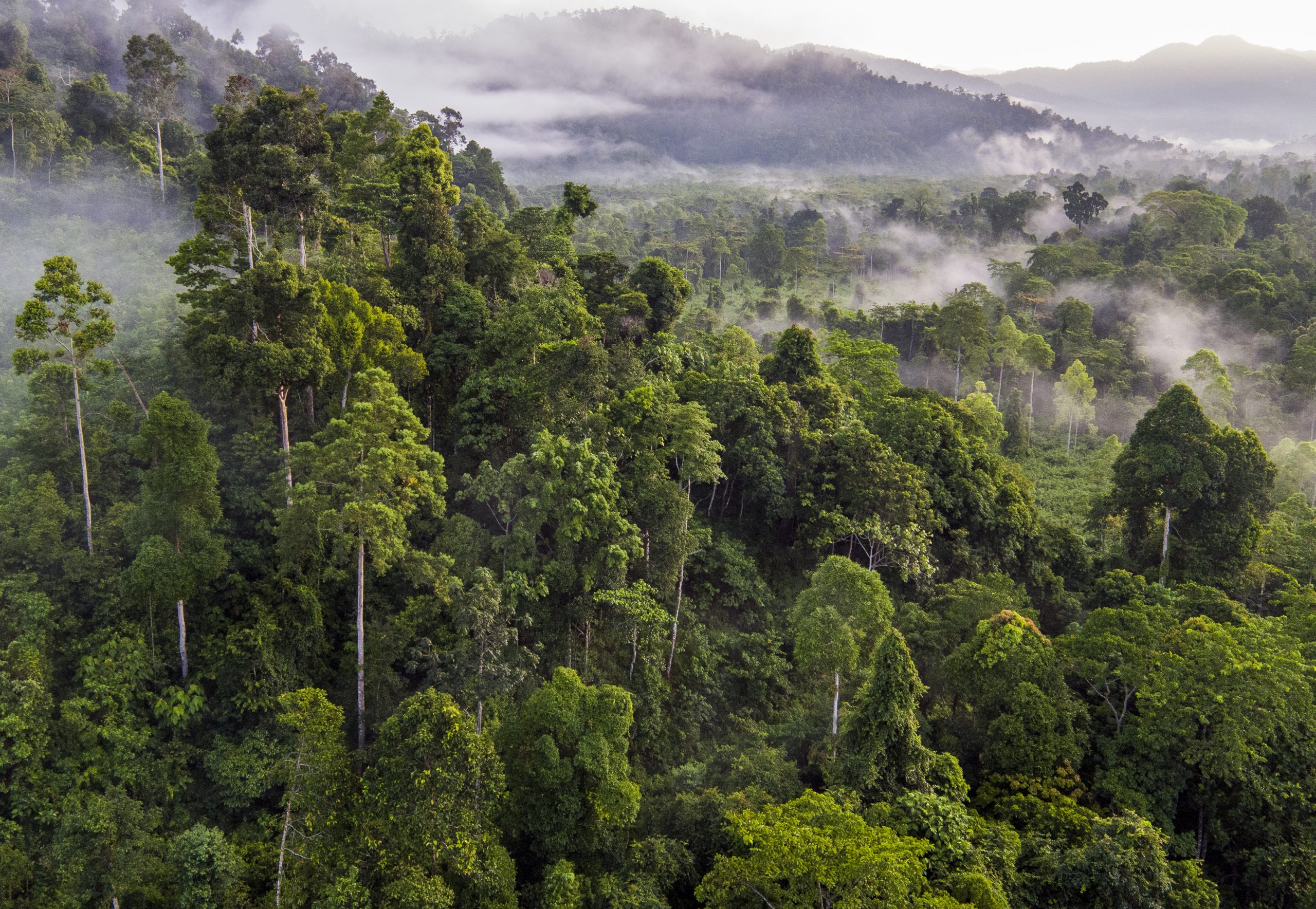
“If we’re going to protect 30 to 50% of the world’s forests, which is what the world’s scientists are calling for, then we have to stop mowing them down to make pizza boxes and T-shirts,” says Nicole Rycroft, founder and executive director of Canopy. “And the only way that we’re going to actually do that is if we have an off-ramp – alternative raw-material inputs to these supply chains that carry a fundamentally lower environmental footprint.”
They are known as “next-gen” solutions – everything from making viscose from the cellulose in old cotton jeans to take-out containers from agricultural residue like straw after a food harvest. We are surrounded by materials that have forest-saving capacities, and harnessing those new raw materials is crucial for us to meet our climate targets. On average, next-gen solutions produce 95% to 130% less greenhouse gases, have 88% to 100% less land-use impacts, and typically use much less water, says Canopy.
Canopy has been working to protect forests for 20 years and now partners with some 900 brands – including fashion giants H&M and Zara, along with publishing stalwart Scholastic and home furnishing icon IKEA – to ensure that the oldest trees remain standing. It has done the deep work of mapping out where these discarded materials are abundant and where facilities such as decommissioned wood mills exist to prime them for second lives.
The targets – like the stakes – are massive. The Audacious investment is intended to help Canopy spur the production of 60 million tonnes of low-carbon next-gen pulp, packaging and viscose by 2030. That, in turn, will alleviate the pressure on trees and enable the protection of 90 million hectares of forest, says Rycroft. It’s not just about the carbon-absorption capacity of forests, but the fact that old-growth trees are vaults of carbon, and releasing that into the atmosphere is the last thing we all need.
If we’re going to protect 30 to 50% of the world’s forests, which is what the world’s scientists are calling for, then we have to stop mowing them down to make pizza boxes and T-shirts.
- Nicole Rycroft, founder and executive director of Canopy
“A lot of people are really surprised to find that there’s more than 300 million trees that are cut down every year to make textiles and clothing,” says Rycroft, like rayon and viscose. “We are looking to transform the relics of the 20th century.”
Canopy’s work falls under three main areas: strengthening the market conditions for next-gen production, scaling that production up, and supporting NGOs on forest conservation.
It’s not just about building a single mill. Canopy will focus on developing six regional hubs – first in India, North America and Europe, followed by Latin America (in particular Brazil), Southeast Asia and China. “You need to actually build the systems that divert clothing from landfill, that actually aggregate the straw, and have there be a standard of fibre quality that is being delivered to the mills,” says Rycroft.
Canopy already has a roster of 35 innovators it is supporting, including ones that are turning microbial cellulose into a viscose fibre “that is stronger than wood and finer than silk.” One of its partners, Renewcell, the world’s first next-gen mill for viscose production, opened in northern Sweden last year, in the bones of an old wood mill.
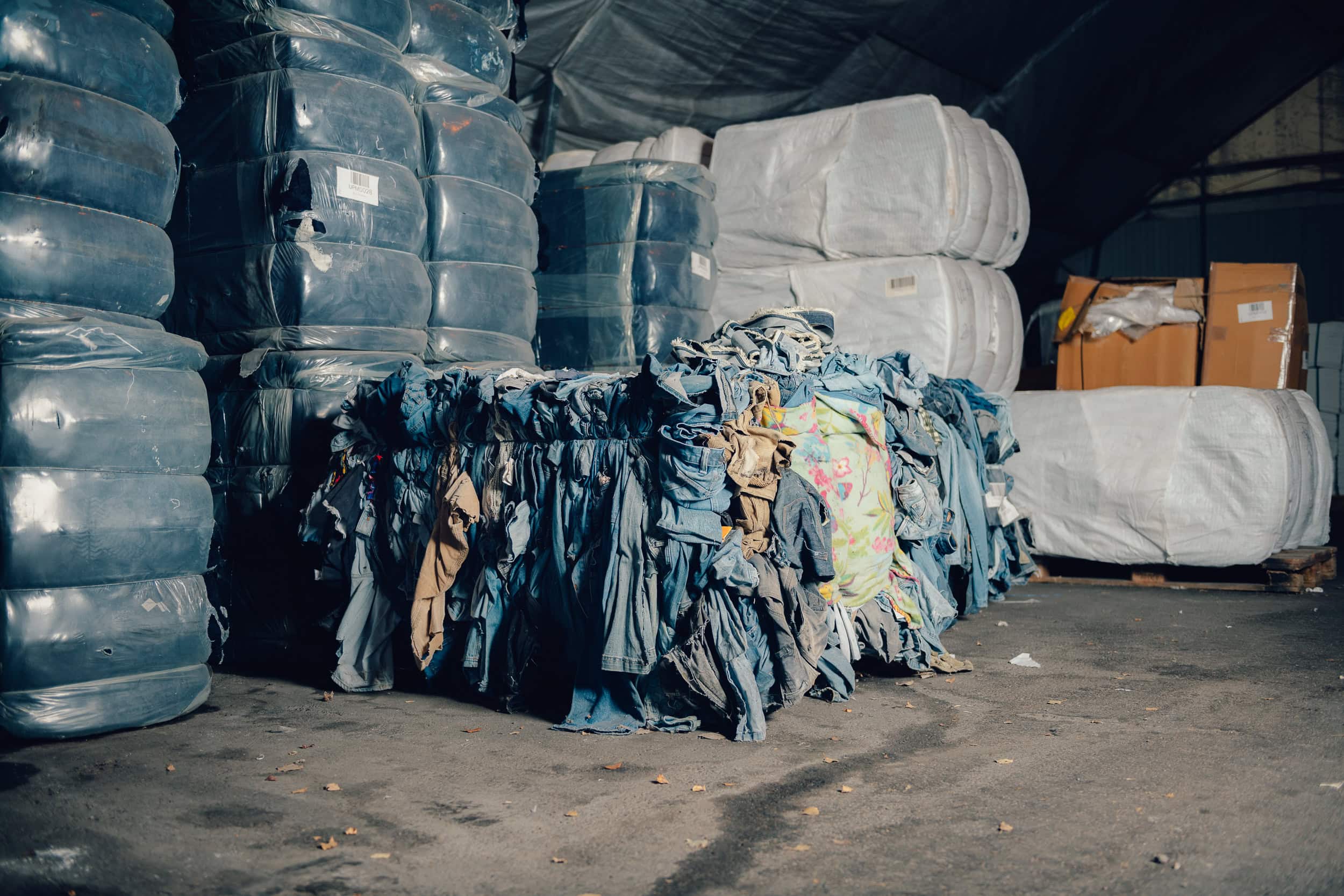
Of course, this transition will take money, and lots of it. Canopy estimates some US$78 billion will be required in new infrastructure and retrofits, and its work includes drumming up investor dollars. But change is happening: the European Union is currently debating whether to ban the destruction of unsold or unused clothing. The proposal is in the EU's strategy for sustainable and circular textiles. Every year, 60 billion items of new clothing end up in landfill within the first 12 months of their production, says Rycroft.
“That’s a lot of fibre for next season’s clothing that is about to come online, so I think we’ll see things change quite quickly,” she says. And not a moment too soon. “We don’t have to wait decades for supply chains to change, and we don’t have that luxury.”